Project Overview
Hey everyone,
This blog is where the Tufts Roboticists team will post updates on our progress on our Intel Cornell Cup Project.
So what is it we’re building?
The Tufts Roboticists team is building a robotic arm intended for use with any mobile robot. We intend to engineer a modular, lightweight, multipurpose arm that will allow almost any mobile robot to interact with its environment.
Making it Multi-purpose
To make the arm multipurpose, we take inspiration from the universal gripper arm, developed by Cornell University:
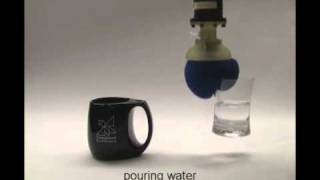
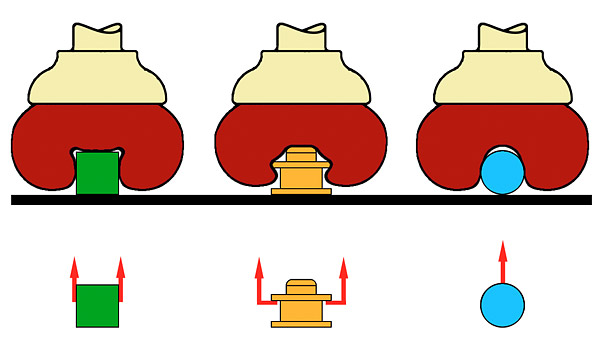
This arm is able to pick up almost any object, regardless of shape. The only constraint on the arm is the amount of weight it can pick up. Thus, this kind of arm is suited to many applications and will enable almost any mobile robot to interact with its environment.
Our goal, then, is to mount this universal gripper on a lightweight arm, better suited to mobile applications than the one in the video. Our design consists of two joints and a rotating base, allowing for horizontal extension up to 60cm. Here’s a video showing our design in motion:
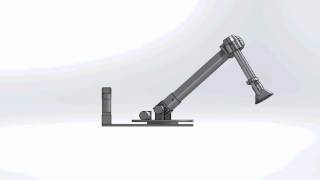
Making it Power Efficient
Another goal of the arm is to reduce power consumption. Cornell’s universal gripper makes use of a vacuum to create negative pressure, allowing the balloon to grip objects. The problem here is that running a vacuum for the duration an object is picked up consumes a lot of power. We have redesigned the system to use a noncompressible fluid (water), a locking linear actuator, and a syringe to create negative pressure. This required that we changed the solid medium in the balloon from coffee grounds (what Cornell used) to fine glass beads, as coffee grounds will dissolve in water. This mechanism only requires energy to remove fluid from the balloon, and once power is cut from the syringe, it (or rather, the attached linear actuator) will lock in place. This means that once an object has been picked up, no more energy need be expended to hold onto it.
Making it Lightweight
Another important factor in the efficiency of the arm is how much weight it has to lift. Ideally, most of the work done by the arm will be put into lifting the target object. This means we must reduce the weight of the arm itself as much as possible. For this reason, the arm is being made from length of 1″ diameter PVC. Additionally, our larger servo motors will be offloaded from the arm, rotating the base plate and the first join of the arm. A smaller, lighter servo is mounted at the upper joint.
What Can It Do?
Our preliminary calculations show that the arm will be capable of the following:
- Arm will be able to lift 2.3 kg before stall
- Arm is 60 cm in length when fully extended
- Base motor has ~50 kg-cm torque
- Upper arm joint has ~45 kg-cm torque
- Full range of motion reachable in 10-15 seconds
- What are your designs?
Here is a system diagram showing all the actuators, how they are controlled, and how they are used:
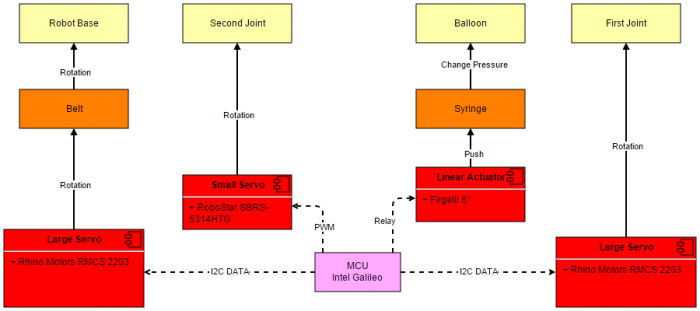
We are currently designing a shield for the Galileo which will have ports for all the actuators to plug into for data. Power will be delivered on separate boards, to protect the Galileo from high currents.
Where are you guys at?
At this point we have received all mechanical parts except a few we need to gear down the servo which will rotate the base plate. We have conducted a proof of concept demonstration of the balloon mechanism with water and glass beads, and found that the mechanism succeeded in picking up objects. We are finishing up a design for a coupling between the linear actuator and syringe. We are also designing the shield for the Galileo which will interface with all actuators. All in all, there is work to be done!