Othermill Exploration
What is a Mill?
A mill is a machine used to cut material using a rapidly spinning cutter. The idea is that the cutter removes material in a process known as subtractive manufacturing. The head of the mill moves based on a computer model, removing material until only the desired model is left.
What is Othermill?
Othermill is a small, portable CNC router manufactured by Other Machine Co. It's intended to be used for producing small components rapidly. It can process a wide variety of materials ranging from waxes and plastics to woods and metals.
Othermill works in the same way as an industrial mill, just on a much smaller scale. It is ideal for home or office use because it doesn't make much noise or take up lots of space. It is also easy to move, weighing just 17 lbs.
How is Othermill useful?
The Othermill machine can be used to rapidly prototype part designs, or to create works of art. Any 3D shape that you can think of, the Othermill can make, provided that it can be carved from top down. A great example of this is creating topographic maps. One of the most useful qualities of the machine is that it can create Printed Circuit Boards (PCBs). Printing a circuit board is a valuable, and often necessary, step when prototyping any type of electronic device.
Goals for the summer
This summer we want to figure out how use of the Othermill can be maximized in an educational setting. More specifically our goals are to:
- Create a training guide for students new to the machine
- Develop training projects which introduce all the features of the machine
- Create a portable workstation that contains everything the mill needs to be used
Project #1: Exploring 3-D Milling Functions
Phase 1: Design
To test the 3-D capabilities of the Othermill, we wanted to test a design that incorporated a variety of topographies. The final design contained slopes, curves and dropoffs with planes meeting at odd angles. On the right are the sketches we decided to test out on the machine to answer the question of how well the Othermill can handle making 3-D shapes.
Phase 2: Modeling and Path Planning
Using Fusion 360, we modeled our final design and worked out the necessary tool paths. The software produces the instructions that we then provided to the Othermill. Below is the final 3D model, made in a CAD program called Onshape. On the left is the rendering of the path the mill will take to create the model.
Phase 3: Operation and Milling
Initially, the imported code did not perform the way we expected. It appeared as though the origins on the tool and the code did not line up. This was eventually fixed by lowering the position of the imported code and allowed us to mill out our piece. The process required a change of drill bits and took a little more than an hour.
Phase 4: Final Product and Conclusion
Event drastically reducing the size of our original design, the milling was a very slow process. In addition, importing the toolpath code was frustrating and quite confusing. However, the Othermill did a great job of contouring the edges and curves to a high degree of detail. As you can see in the picture to the left, the mill was able to handle sloped surfaces and curves to replicate our model very well.
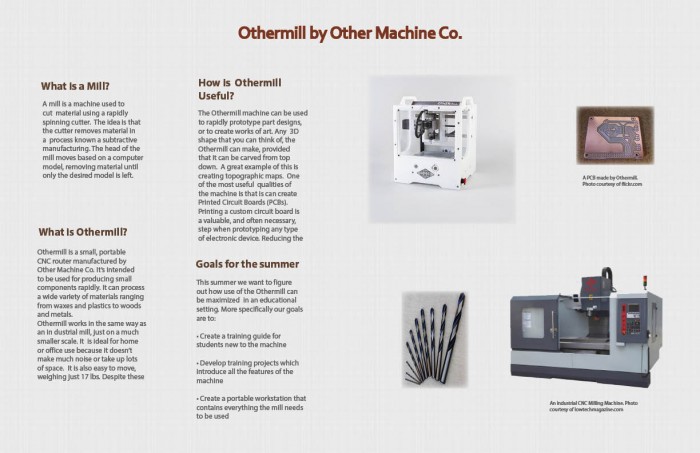
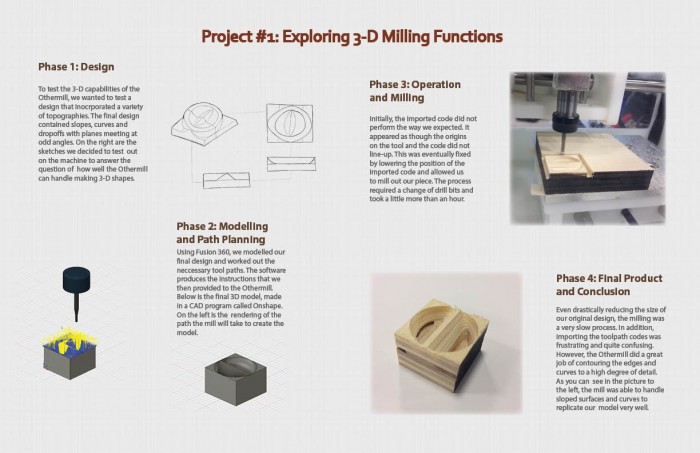