Tufts TIHRA: Tele-operable in-home Robotic Assistant
(Originally from here)
About
We are a group of mechanical engineers from Tufts University, who are working on building a tele-operable soft robotic manipulator and arm to assist a quadriplegic person with daily activities. We are currently involved in the RoboSoft Grand Challenge, competing in the manipulation challenge.
People
Whitney Crooks
Whitney Crooks is a PhD student in mechanical engineering.
Gabrielle Vukasin
Gabrielle Vukasin is a Master’s student in mechanical engineering.
Maeve O'Sullivan
Maeve O’Sullivan is an undergraduate student in human factors engineering.
First Prototype
The beginning
My PhD project evolved over the course of the past several years of work with my advisor, Dr. Chris Rogers. Knowing that I’d long been interested in both soft robotics and assistive robotics/prosthetics, Chris and I began working with Dr. William (Bill) Messner on a user interface that would enable mobility impaired individuals (think the elderly, quadriplegics, those suffering from muscular degenerative diseases, etc.) to lead more autonomous lives. Our work started with Baxter, focusing on what grippers Baxter would need to help these individuals as well as how the user would interact with the robot.
We quickly came to the realization that Baxter, while an excellent platform in many situations, was not quite ideally suited as an in-home robotic assistant. We needed to make our own robot. This realization occurred around the same time that the RoboSoft Grand Challenge was announced, and we thought, what an excellent forum around which to develop our robot.
Over the past semester, I recruited two team members from the Tufts University community: Maeve and Gabby. Maeve is an undergraduate human factors student passionate about user interfaces and developing human-centric devices. Gabby is a master’s student in mechanical engineering interested in controls developing autonomous robots. Together, we make up a three-person team working hard to ensure we have the best robot possible to compete in the RoboSoft Grand Challenge.
Gabby, Maeve and I have been working hard over the last few months, researching and developing ideas for our Teleoperable In-home Robotic Assistant, or TIHRA. After reading countless papers, and discussing many options, we decided on tendon-driven actuation.
The finger
The question was then what materials to use for the hand of our robot. We decided on Dragon Skin, a castable silicone elastomer that can stretch ~600%. For our first prototype, we cast the finger as a flat rectangle and embedded toothpicks in the Dragon Skin to act as ribbing, providing support for the finger without compromising the softness and flexibility. We embedded a string near the top of the finger, that when pulled, causes the finger to bend. We rolled up the finger and taped it into a cylinder (the plan was to seal the finger with Dragon Skin but we were just too excited to see whether or not it worked).
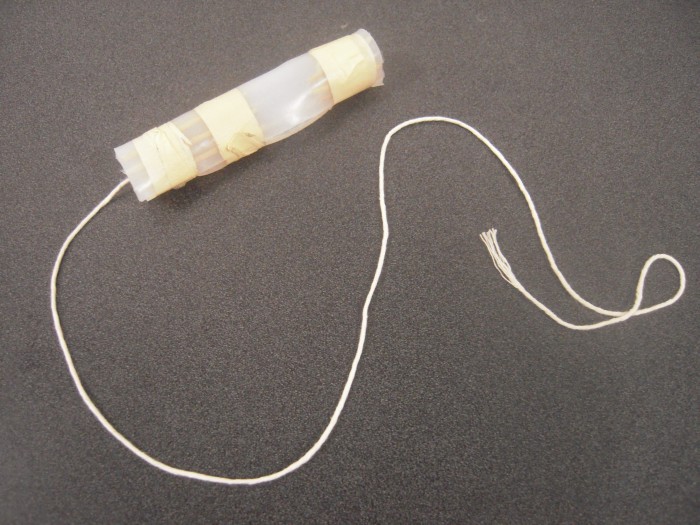
The first prototype of our finger for TIHRA
We were pleased with the results of the first finger, but thought it might be better and easier to cast the finger in a cylindrical shape. We already have several prototypes built so stay tuned.
The arm
The prototype for our arm was developed by Marc and Anna, two undergraduates from Spain who spent the summer with us at the Center for Engineering Education and Outreach (CEEO). They built a robotic arm actuated by three servos (two to control the arm position and one for the gripper position) that could be attached to an omniwheeled platform that was controlled by three servos (one for each wheel). All servos could be controlled with a single joystick.

Marc demonstrates how to control his and Anna’s arm design
Our final arm will take inspiration from this first prototype. We were pleased with the degrees of freedom Marc and Anna’s design afforded us, but we would like to scale up the robot and increase robustness.
What's next?
Stay tuned for more posts on our progress. Up next is our second finger protoype and first prototype of our hand, but in the meantime, checkout our YouTube video and technical document!
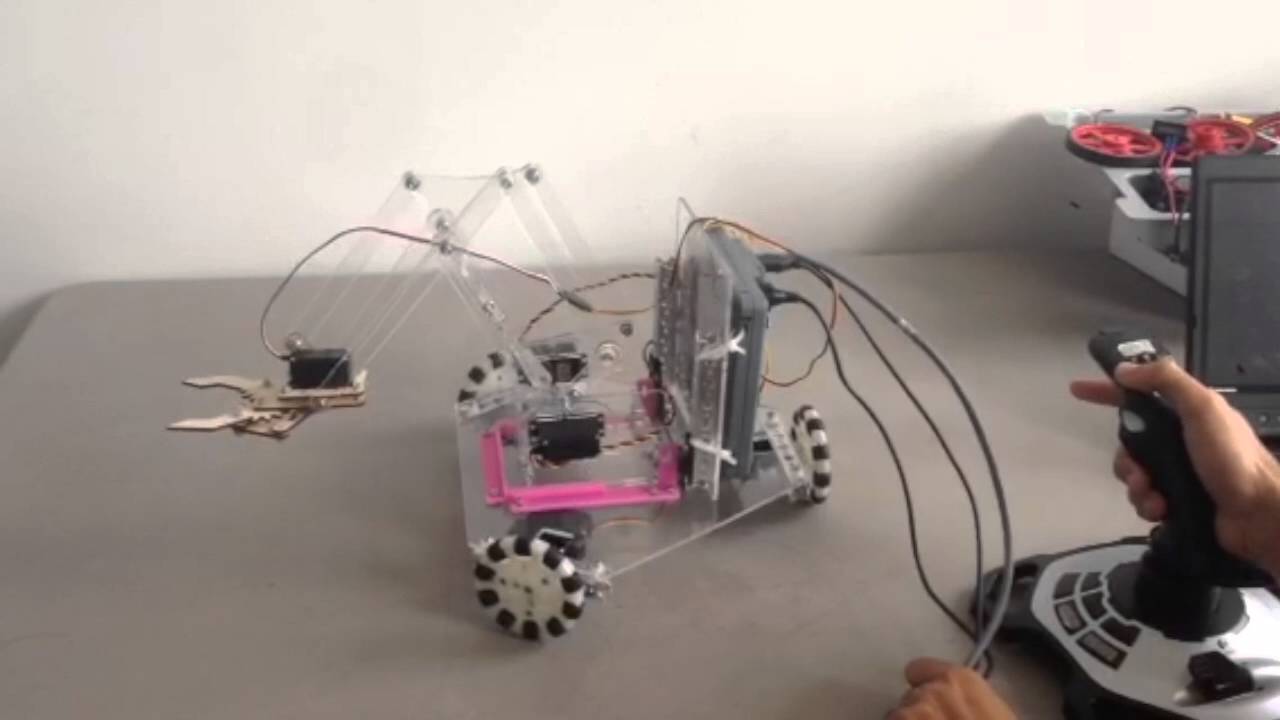
January 6, 2016 Update: Second prototype
In between holidays and enjoying the unseasonably warm weather, Gabby, Maeve, and I have found time to work on TIHRA. When we last left you, we had just finished our first prototype for our finger. Well, since then we’ve made some improvements, and we now have a second prototype to show off.
Our second attempt at making fingers for TIHRA involved casting Dragon Skin inside 3/4″ inner diameter (ID) PVC pipes, which we used as molds. The strings, or tendons, were inserted into a straw, both of which were inserted into the molds prior to casting.
This method produced pretty good results. We were pleased with the casting technique, but would like to better control the bending point, or joint, in the finger.
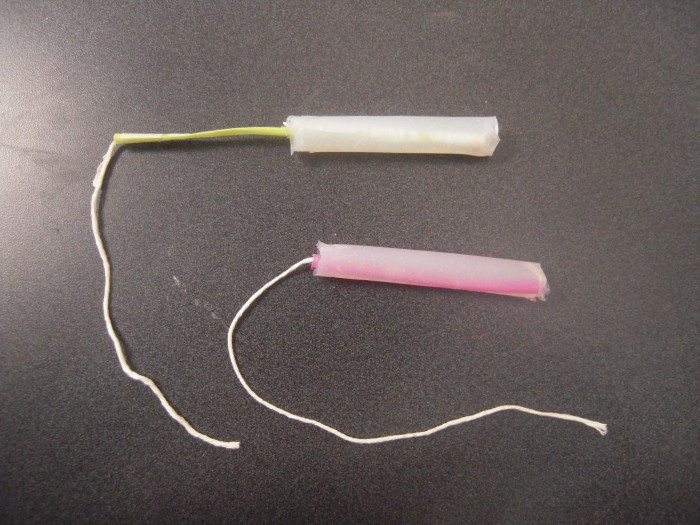
Two TIHRA fingers. Fingers are made from Dragon Skin cast inside of PVC pipes. String-like tendons inside a sheath are inserted into the molds prior to casting.
We placed three of the best fingers into a 3D printed base and hooked up the tendons to Digilent DC motors. The motors were plugged into two Digilent motor boards, which were attached to a myRIO. A simple code was written to open and close the hand. We’re also working on PID control.
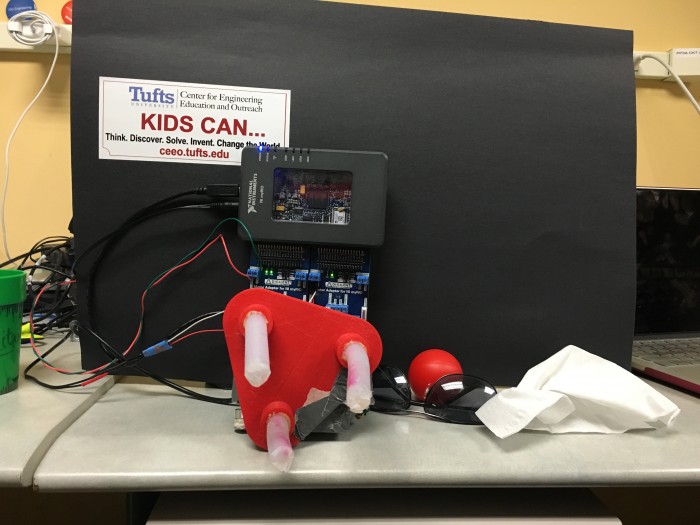
1st prototype of TIHRA hand shown with myRIO, Digilent motor drivers, and Digilent motors.
Check out our latest YouTube video and technical document, and stay tuned for more updates!
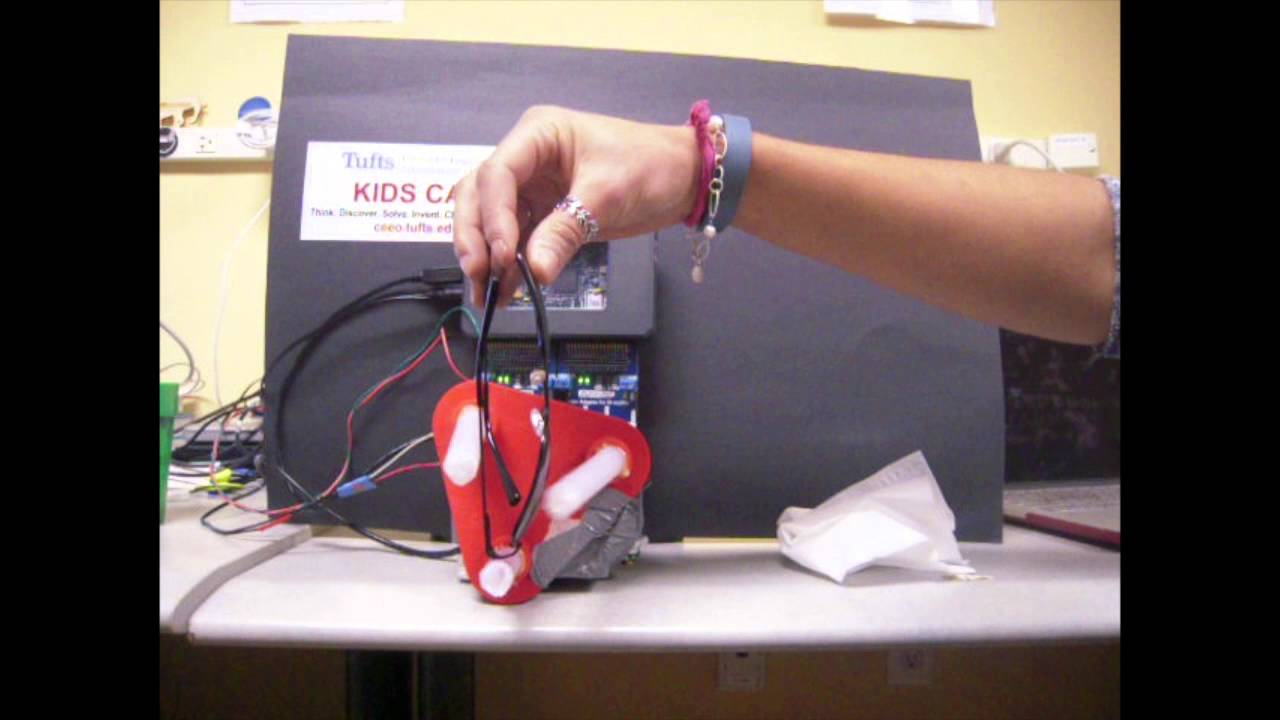
February 29, 2016 Update: Third prototype
The Tufts TIHRA team has been hard at work for the past two months redesigning and testing and redesigning and testing. Since we last wrote, our team has been learning as much as we can about how hands work and sifting through different robotic designs for inspiration. The question that we keep coming back to has to do with actuation: do we want to push or pull our fingers to create a grip? Throughout the past two months we’ve been shifting back and forth and back and forth, push or pull, push or pull, and finally, I think, we’ve landed somewhere in the middle.
The human hand meets the robotic hand
In order to better understand our first prototypes and our design rational, I want to tell you a little bit about the human hand.
About a month ago, I attended Janet Brooks’ occupational therapy class on hands, and until a month ago, I had no idea that you could give a three hour class on tendons in the hand. You can, and you can also make it super interesting. I’m going to dumb it down a lot, so forgive me if you’re Janet Brooks or Charles Cassidy, a hand surgeon I also spoke with.
You can think of the hand as having two sets of tendons: the set on the palm-side of your hand that pull the fingers in (flexor tendons) and the set on the back of your hand pulling the fingers back out (extensor tendons). Check out the image below to see for yourself (E in EDC and EIP is extensor and F in FDP and FDS is flexor). A tendon affects any joint it runs over but most significantly the last joint is passes over. These two sets of tendons act in opposition of each other, which is why your hand rests in a half-grip state. The majority of the tendons are actuated by muscles in your forearm.
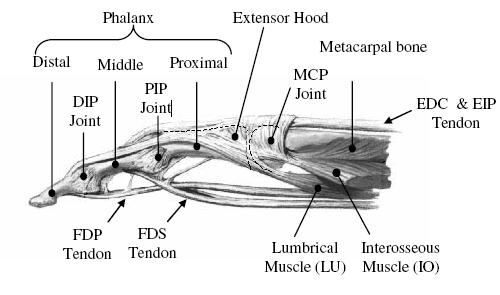
Bundhoo, V., & Park, E. J. [2005, July]. Design of an artificial muscle actuated finger towards biomimetic prosthetic hands. In Advanced Robotics, 2005. ICAR’05. Proceedings., 12th International Conference on [pp. 368-375]. IEEE.
So if you think about our finger in the context of the human finger, we have a flexor tendon acting as a combination of the FDP and the FDS in order to pull the finger into a grip and a motor acting as the muscle responsible for that action. Our extension, unlike the human finger, is passive and relies on the material properties of the silicone in order to return it to it’s extended state. Another difference is that our soft finger acted as a continuum where as a finger as distinct joints.
The dilemma: to redesign or not to redesign
So maybe you’ve seen the YouTube video from the previous post, and you’re thinking (or at least we hope you’re thinking), “Pretty cool. Why redesign?” Well, here’s the problem: in order to add the structure we think our finger needs for strength and to ensure bending around the correct access, we either need to add a hard (or at least stiffer) exoskeleton or change our manufacturing process. Executing the former, means straying from our goal of a soft manipulator, and choosing the latter would require a more complex manufacturing process that we’ve already had limited success with. Additionally, we were worried about the repeatability of both the current and proposed manufacturing process.
We did make another set of soft fingers, modifying our manufacturing process slightly to ensure the tendon was embedded where we wanted it to be and the finger would bend how we wanted it to. These fingers worked much better than the previous sets, but we still weren’t satisfied…
So we redesigned
One of our advisors, Bill Messner, has been working with an undergraduate named Shane on a passive gripper (a gripper that needs actuation to release) inspired by the Festo MultiChoice gripper, which uses Fin Ray Effect technology developed by EvoLogics. The Fin Ray Effect gripper is simple and elegant, made of flexible material, and adapts to objects it encounters. Check out the video. It’s pretty cool, and Festo builds a great product.
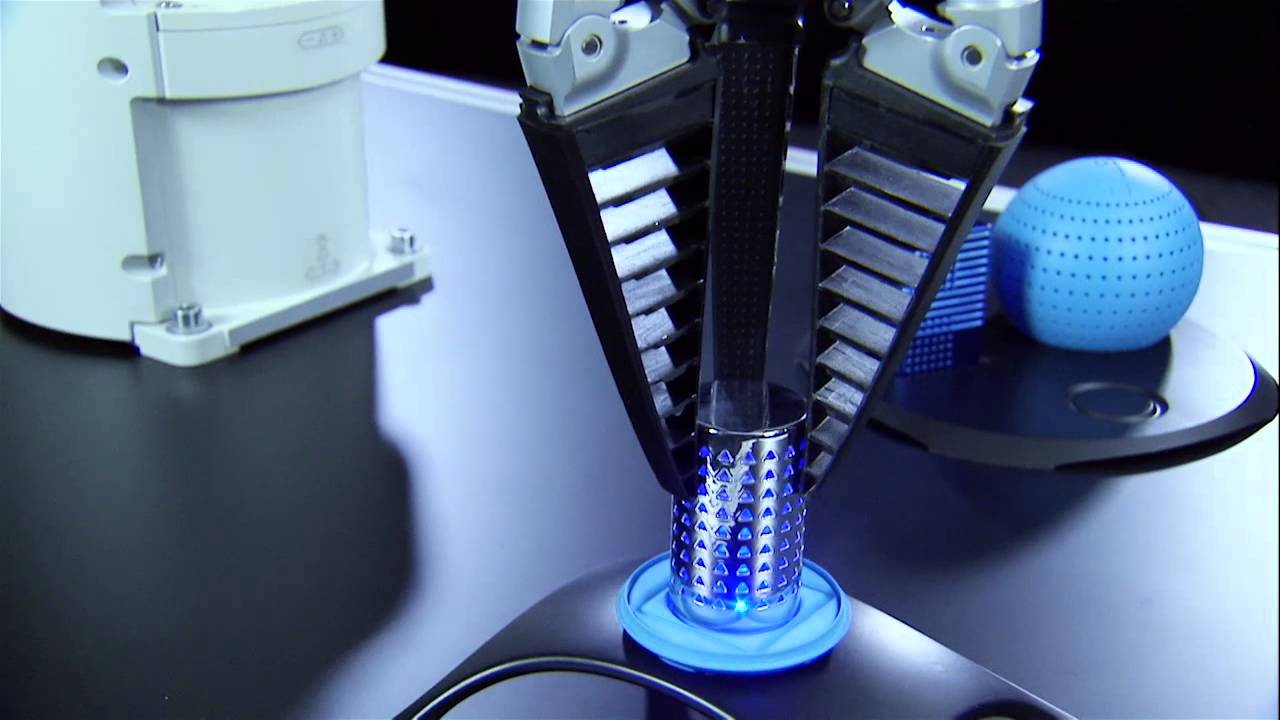
We modified their gripper a bit and 3D printed molds to cast the Dragon Skin in. The fingers were a success! Check out the pictures below, our CAD drawing, and our new YouTube video.
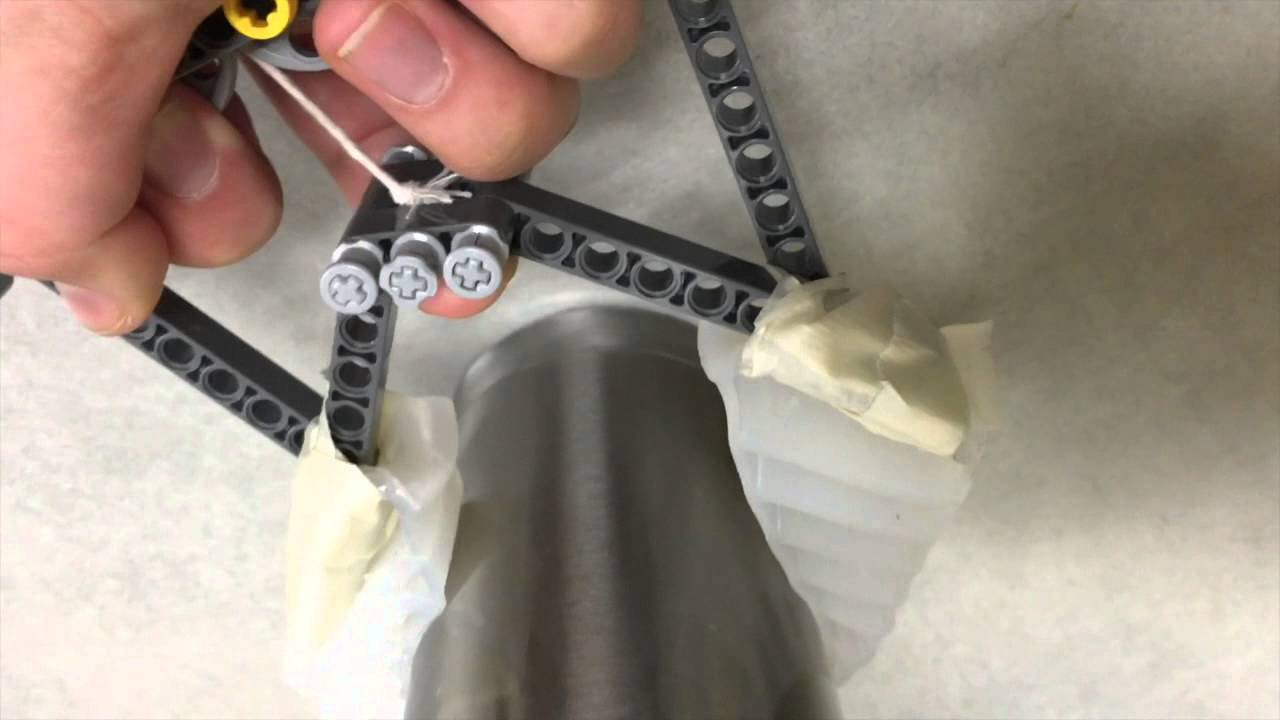

Fin Ray Effect inspired fingers
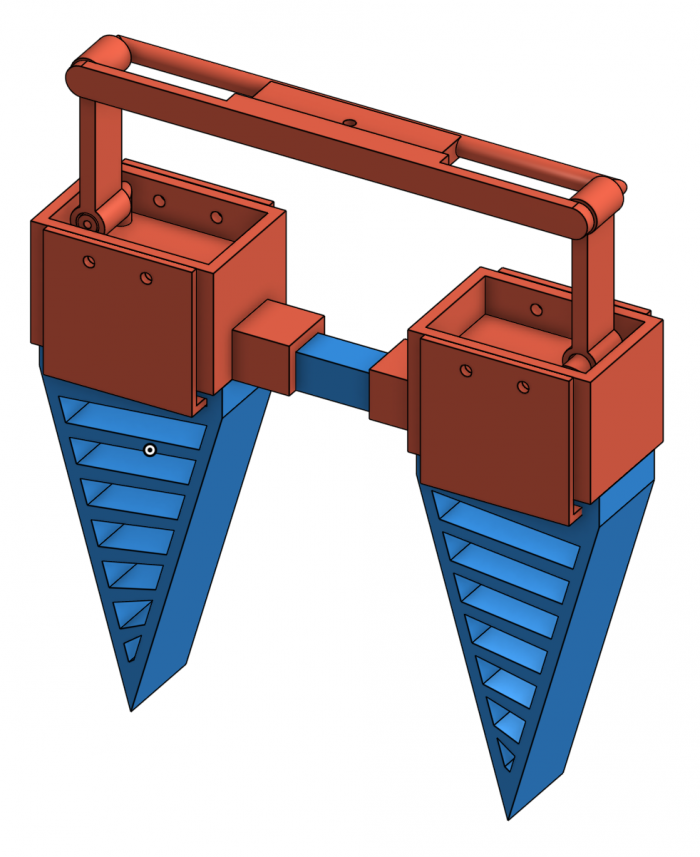
Design for a soft hand with the Fin Ray Effect inspired grippers
As always, stay tuned for more updates!
March 8, 2016 Update: Putting the hand on Baxter: take 2
Last week, I told you that we redesigned TIHRA’s fingers and linked you to a YouTube video showing the fingers on the Baxter. This week, I’m going to link you to a new video.
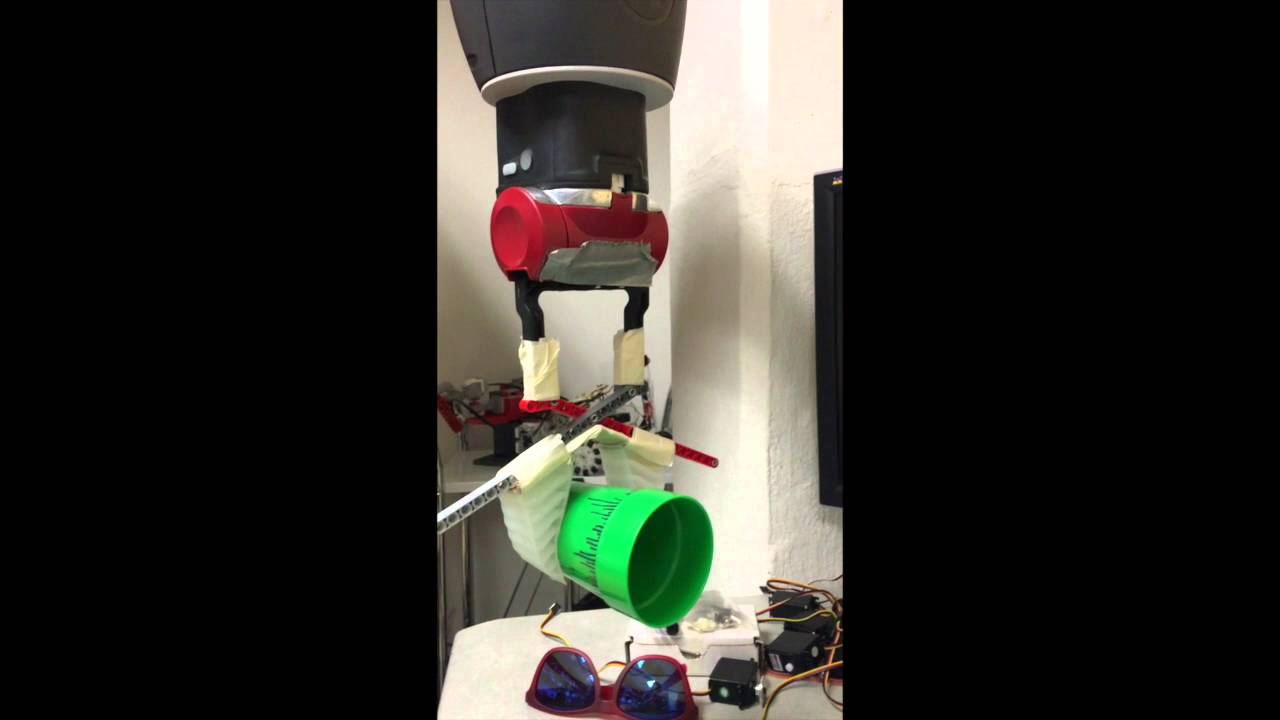
We realized after putting the video on Baxter, that we weren’t getting the correct motion. The fingers should be pivoting as they move together rather than just move together. So to get the wanted effect, I taped some LEGOs to Baxter and the fingers. These LEGOs provide a scissor motion so that when Baxter’s grippers close, the “scissors” close, causing the soft grippers to pivot inwards.
It’s a short update, but stay tuned for some exciting new prototypes coming your way!
May 23, 2016 Update: The RoboSoft Grand Challenge
A few weeks ago, TIHRA participated in the event we’ve been preparing for: the manipulation portion of the RoboSoft Grand Challenge.
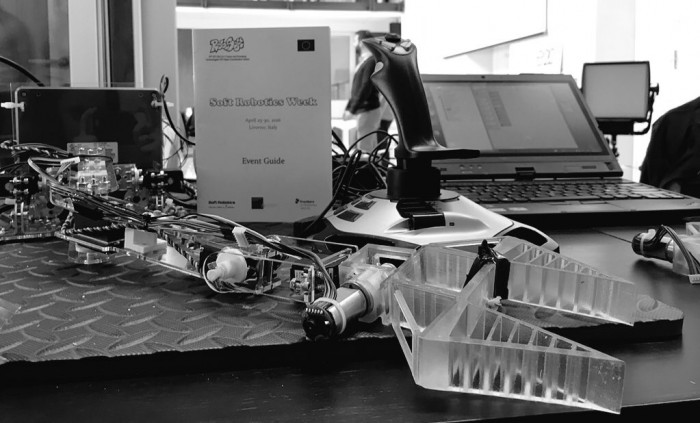
The Challenge was a great opportunity for us to interact with teams from across the globe, learning from their successes and failures, and for us to test TIHRA outside of the lab. It was pretty cool to see the diversity of solutions and interact with the creators of the different robots.
TIHRA performed worse in the pick and place task and better in the reaching task than we thought. We were able to pick up the ice-cream cone and able to reach the other objects but not able to pick up them up for a few reasons. The tupperware was difficult to get a good grip on, the wrench fell out of the fingers, and the waterbottle was too heavy for the gripper. However, TIHRA performed better at reaching the objects than we expected, able to touch two of the three objects, and we were very close to succeeding at the entire task. TIHRA was unable to complete the third task, which was opening a door. We were able to grip the handle but not able to provide enough force to turn the handle.
This whole experience left us with a few take-aways:
- There are a lot of universities out there doing some really cool soft robotics stuff. Shout out to the BioRobotics Institute at Sant’Anna, Bristol Robotics Laboratory, DEFROST at INRIA, Biologically Inspired Robotics Laboratory at Cambridge.
- The gripper needs to be improved to increase strength and prevent deflection when the gripper is picking up an object.
- Redesign the arm so that it is soft or compliant.
If you want to see TIHRA and action, check out our new video on YouTube or below!
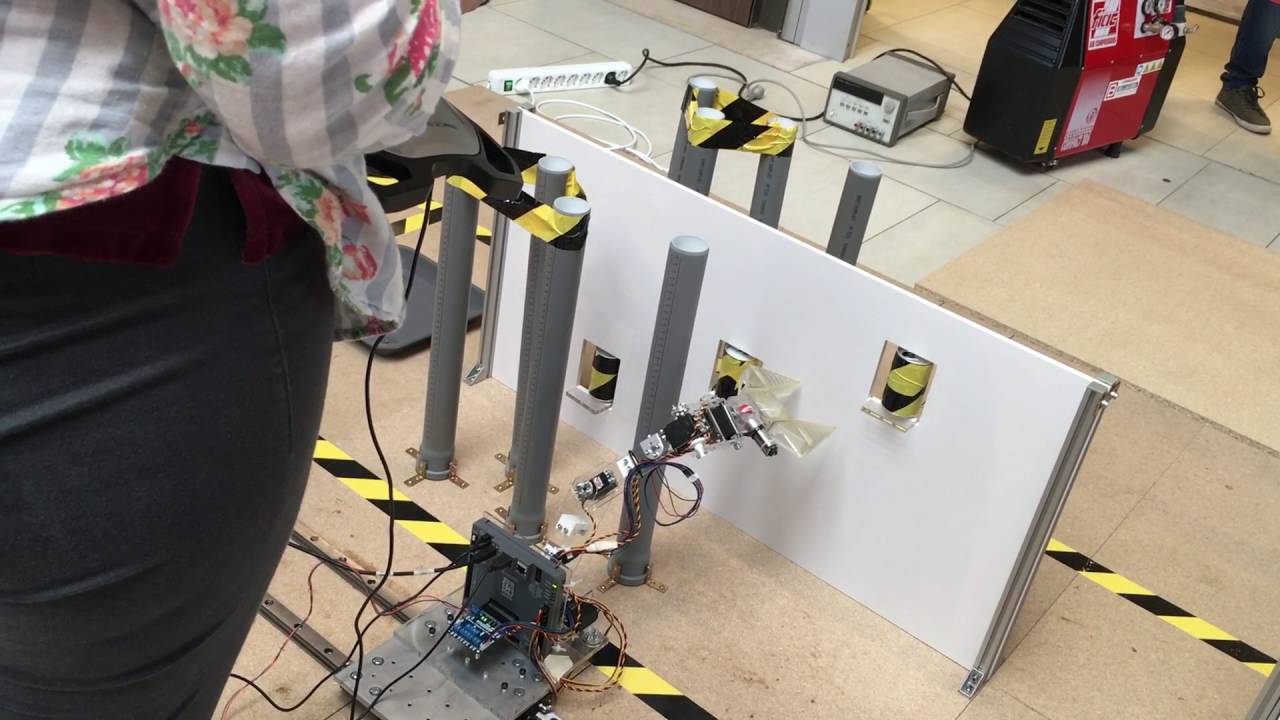